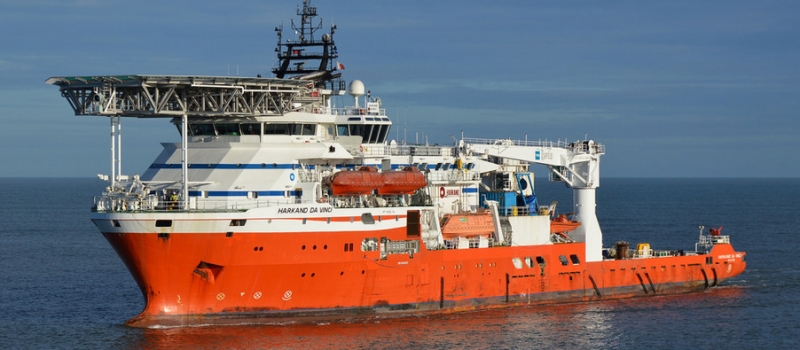
Electric drives have become increasing popular for commercial vessel propulsion, including cruise liners, oil and LPG tankers, survey vessels, drilling rig supply tenders and specialist ships for a range of duties.
Electric drives and motors offers benefits, including higher fuel efficiency, ease of control, more equitable use of space and more manoeuvrability, especially where azimuth or podded propulsion is installed.
Warships share the majority of the above benefits. However, additional benefits include reduced life cycle and procurement costs, improved survivability, reduced signatures (acoustic, infrared and magnetic), increased range and endurance.
The six Royal Navy’s Daring Class, Type 45 destroyers, were the world’s first “electric warships” with 2 x 20MW 4.16kV, multi-level PWM main propulsion drives and 15 phase propulsion motors.
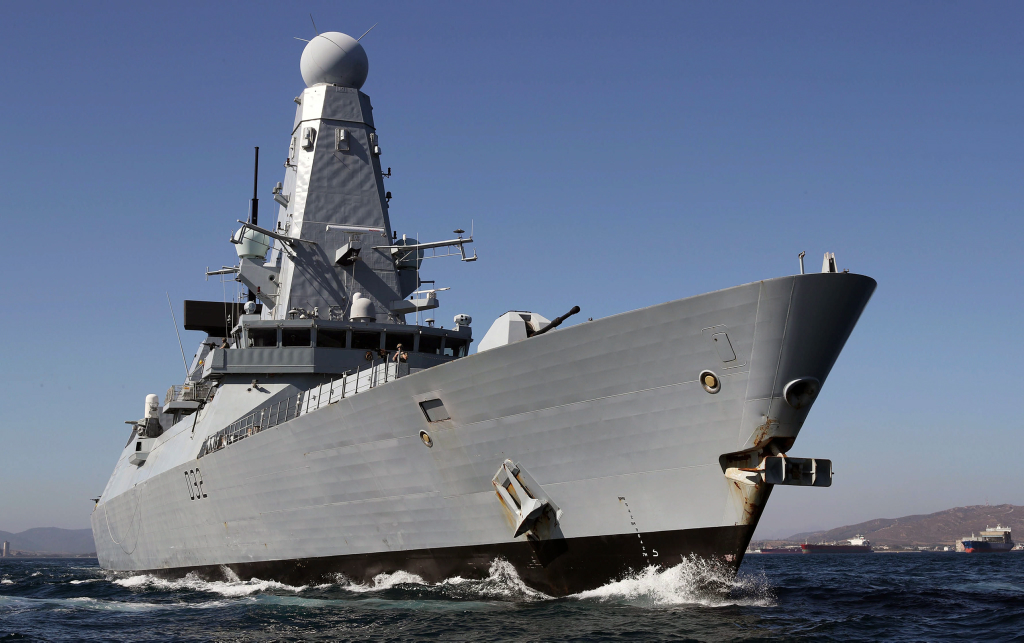
One of the main considerations when considering ‘conventional’ AC marine propulsion drives is the physical size of the drive and other propulsion equipment. For, example, the two 20MW PWM drives and ancillary equipment currently installed in the Royal Navy’s Type 45 destroyers require 35.2 cu.m. of space each (including the input passive filters and the sinus filters between the drives and the motor). The physical size of the main propulsion system(s) often determines the available space for cargo or the amount and type of weapons and associated systems in warships.
Another serious consideration is total harmonic voltage distortion (THDu). To reduce the THDu, conventional propulsion drives include phase-shifting transformers and/or passive or active harmonic filters or so called AFE (active frond end) rectifiers. Even when all precautions are taken to reduce the harmonic current drawn by the drive converters, the harmonic voltage distortion can still be in excess of the standards or marine classification body rules due to the switching of the power devices.
The benefits of Resonant Link soft-switching technology for marine propulsion systems
- Very high-power density around 5.5MW per cu.m. This is over 80% less than PWM drives.
- High efficiency (>98%). Soft switching enables inversion up to 20kHz switching with resultant high efficiency at MV.
- Virtual elimination of harmonics with THDi (total harmonic current distortion <1% at input and <1% THDi at output for any conversion, AC or DC). Sinusoidal voltages and currents at input and at motor.
- The elimination of conventional transformers for voltage transformation and galvanic isolation, thus saving considerable weight and space. Direct connection to MV.
- No additional harmonic or EMC filtering is required compared to conventional drives reduces physical size and weight.
- Voltages, AC and DC can be transformed without conventional transformers.
- Propulsion motors and ships generators are, for example, subject to only dv/dt (i.e. rate of rise of voltage) of <20V/μs on 4.16kV (compared to 30,000/μs for conventional PWM drives) thus eliminating insulation failure, bearing erosion, cable resonance and common mode voltage and other EMC issues.
- Fault immune operation via natural fault current limiting and zero current turn off. No expensive AC and DC circuit breakers are required.
The installation of Resonant Link propulsions permits more cargo space on commercial vessels. On warships, more space will be available for additional high energy weapon systems including rail guns, lasers and defensive armour; indeed, a multi-port Resonant Link converter can supply these electric weapons and drive the main propulsion.
Note : It is also possible to install a Resonant Link DC power systems for main propulsion duty on vessels which utilise conventional PWM drives for propulsion. For retrofits, the normal input rectifiers and DC bus capacitors can be removed and the DC voltage for PWM IBGT inverters supplied through the Resonant Link common DC bus or DC ring main. See section on Marine DC Systems. For new installations, only the VFD IGBT inverter sections have to be purchased from the drive manufacturer not the complete PWM drive.