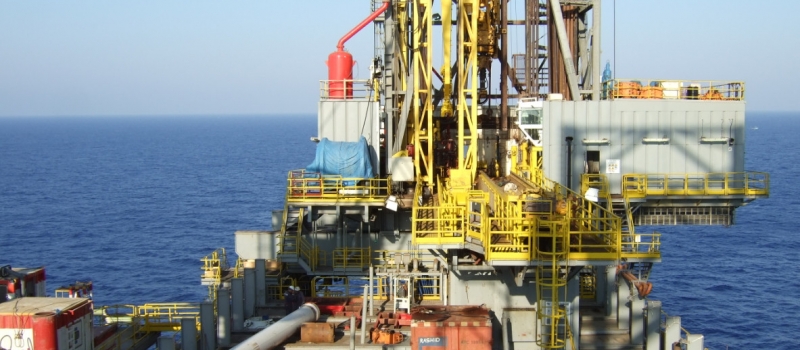
The more modern MODUs (mobile offshore drilling units) tend to utilise large AC variable frequency (VFDs) in the ‘drilling package’ (mud pumps, draw-works and top drive).
Offshore production platforms also utilise VFDs for a range of duties including compressors and electrical submersible pumps (ESPs).
New installations of both types of installation can benefit significantly from a Resonant Link AC-DC active transformer common DC bus or DC ring main system, as introduced in the section of Marine DC power systems. Instead of complete VFDs (i.e. rectifier, DC bus and IGBT inverter) only the VFD IGBT inverters are required to control the drive motors.
An example of DP3 dynamically positioned drilling rig with a 6kVDC ring main supplying 8 off 4.16kV, 3200kW thruster VFDs and a separate common DC bus for the drilling package on a LV (600VDC) VFD drilling package can be seen below.
Salient benefits of the using Resonant Link DC power for drilling rigs
- Extremely compact design of AC-DC active transformer(s) (5.5MW per c.u.m.) compared to conventional power conversion technologies. Space and weight are important factors for equipment offshore.
- The negation of conventional transformers frees up important space. (The ~5.5MW per cu.m. stated above includes the nanocrystalline transformer(s) which weigh ~ 45kg per MVA).
- Virtually no harmonic voltage distortion (THDu) due to <2% THDi at input. No DC ripple.
- No additional protective equipment (i.e. AC and DC circuit breaker) required further reducing cost.
A Resonant Link DC power system yield a significant reduction in the total VFD footprint on production platforms and other installations compared to conventional VFD installations with virtually zero harmonic voltage distortion.